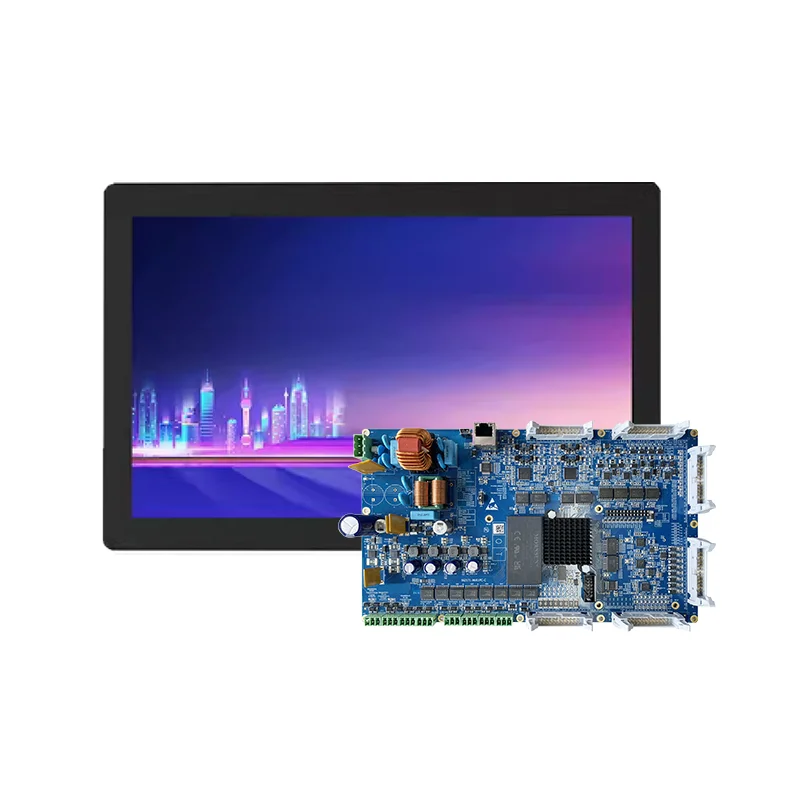
How Do DAQ Systems Transmit Data to Computers?
In today’s technology-driven world, data is everywhere. From precision testing in R&D labs to quality control on production lines and field-deployed monitoring systems, we rely on converting signals from the physical world into digital data that can be analyzed and processed by computers. Data acquisition (DAQ) systems play a crucial role in this process. Acting as a bridge between the physical and digital realms, DAQ systems measure physical phenomena—such as temperature, pressure, voltage, or sound—and convert them into digital signals that computers can understand.
But how exactly do DAQ systems efficiently and accurately transmit large volumes of data to computers? This article dives into the mechanisms of data transmission in DAQ systems, helping you understand the flow of data and how to choose the best DAQ solution for your application.
1. The Data Bridge: A Detailed Look at DAQ Interface Technologies
The transmission of data between DAQ systems and computers relies on various interface technologies. These interfaces act as bridges, enabling stable and efficient data flow from DAQ hardware to a computer. Each interface has unique advantages in speed, range, cost, and ease of use. Here are several widely used and critical DAQ transmission interfaces:
1.1 USB (Universal Serial Bus): The Popular Choice
USB is one of the most common DAQ interfaces today due to its:
- Plug and Play: Easy to use with no complex configuration required.
- Convenient Power Supply: Many USB DAQ devices can be powered directly through the USB port, eliminating the need for an external power source.
- High Availability: Almost all modern computers are equipped with USB ports.
- Data Transfer Speed: USB 2.0 offers a theoretical bandwidth of 480 Mbps, while USB 3.0/3.1/3.2 increases bandwidth to several Gbps. USB4 further boosts it to 40 Gbps—more than sufficient for most low- to mid-speed data acquisition applications.
Data Transmission Mechanism: USB DAQ devices communicate with the host via polling or interrupt methods. Data is buffered and transmitted over the USB bus under the control of the USB controller.
Application Scenarios: Ideal for portable measurements, lab testing, and educational or research scenarios where ease of use is essential.
1.2 Ethernet/LAN: The King of Long-Distance Transmission
Ethernet is a preferred interface in industrial and distributed measurement systems due to:
- Long Transmission Distance: Ethernet enables data transmission over hundreds of meters, ideal for remote monitoring and distributed systems.
- Network Integration: Multiple DAQ devices can connect to the same network for data sharing and centralized management.
- Strong Noise Immunity: Designed for industrial environments with stable and reliable data transmission.
- High Speed: Gigabit Ethernet offers 1 Gbps bandwidth, while 10 Gigabit Ethernet reaches up to 10 Gbps—suitable for high-speed, multi-channel data
Data Transmission Mechanism: Ethernet DAQs typically integrate TCP/IP stacks, packaging data into packets for transmission. Computer software receives and decodes these packets via network interfaces, enabling routing and flexible topologies.
Application Scenarios: Industrial automation, structural health monitoring, large equipment testing, and remote monitoring.
1.3 PCI/PCIe: The Backbone of High-Performance DAQ
PCI and PCIe are internal computer buses built for applications that demand ultra-high throughput and minimal latency:
- Ultra-high speeds: PCIe 3.0 x16 supports up to 128 GB/s, with PCIe 4.0 offering even higher throughput.
- Low latency: Direct internal connection to the computer’s motherboard ensures minimal delay.
- High stability: Internal connections are less susceptible to environmental interference.
Data Transmission Mechanism: PCI/PCIe DAQ cards are inserted into computer expansion slots, with their controllers communicating directly with the CPU and memory. Leveraging DMA (Direct Memory Access), data is written directly to memory, minimizing CPU load and maximizing transfer efficiency.
Application Scenarios: Aerospace, automotive testing, scientific experiments, and high-speed data logging.
1.4 Wireless: A Flexible Emerging Solution
Wireless DAQ systems are gaining popularity, offering enhanced flexibility and ease of deployment:
- High Flexibility: Cable-free deployment, ideal for hard-to-wire or dynamic environments such as vibration monitoring on rotating machinery or remote field monitoring.
- Strong Mobility: Suitable for mobile measurements or distributed deployments, allowing sensors to collect data far from the receiver.
- Easy installation: Minimizes cabling work, reducing installation time and cost.
Data Transmission Mechanism: Wireless DAQ systems use Wi-Fi, Bluetooth, or cellular networks (e.g., 5G) to send data to computers or cloud platforms. Wireless transmission may suffer from environmental interference, making it more suitable for applications with lower data volumes and relaxed real-time requirements.
Application Scenarios: Environmental monitoring, remote systems, agricultural IoT, and contactless measurements.
2. Smartgiant’s DAQ Products
With a better understanding of USB, Ethernet, PCIe, and wireless technologies, it’s clear that DAQ solutions must be tailored to specific needs such as resolution, speed, and deployment conditions. Smartgiant’s DAQ products are based on deep innovations in these interface technologies, offering solutions for high-frequency data, modular expansion, and industrial networking.
2.1 SG1227 PCIe Data Acquisition Card
The SG1227 is a high-speed 8-bit dual-channel PCIe DAQ card offering up to 5 GSa/s sampling rate and 500 MHz analog bandwidth. Key features include:
- Programmable FPGA (Xilinx XCKU040):Enables real-time data processing and custom algorithm deployment—ideal for demanding applications such as radar and LiDAR.
- High-Speed Data Transfer: An 8-lane PCIe 3.0 (x8 Gen3) interface delivers data to the host at up to 1.25 Gbps, ensuring low latency and high reliability.
- Flexible Clocking and Triggering: Supports internal 100 MHz reference clock, external 100 MHz reference clock, external 2.5 GHz sampling clock, and external trigger I/O for precise data capture.
- Waveform Visualization: Allows real-time display of time-domain and frequency-domain waveforms on the host computer for convenient monitoring and analysis.
Application Scenarios: In ultrasonic flaw detection, it captures echo signals at 2.5 GS/s and uses FPGA-based defect localization with 0.1 mm accuracy.
2.2 High-Speed DAQ Module
High-speed DAQ module is a modular, dual-channel 12-bit DAQ unit supporting up to 125 MS/s with dynamic gain adjustment (1–1000x). It features LVDS bus and FPGA acceleration, ideal for new energy motor testing and semiconductor equipment.
- 12-bit ADC with 125 MSps sampling, 300 MHz bandwidth, and 60 dB SNR.
- Dual-channel input, supporting multiple signals.
- FPGA real-time processing, offloading the host computer.
- Compact and low-power design (12W), suitable for embedded systems.
Typical Application Scenario – New Energy Motor Testing: 125 MSps sampling rate for capturing high-frequency PWM drive signals, dual-channel synchronized monitoring of current and voltage, and FPGA-optimized spectrum analysis.
2.3 SG2168 High-Speed DAQ Box
SG2168 is a dual-channel 14-bit edge-computing DAQ device with 500 MS/s per channel and 200 MHz analog bandwidth. It integrates a Xilinx MPSoC and industrial protocol interfaces for smart infrastructure.
- Multi-Protocol Communication Matrix: Gigabit Ethernet, CAN FD/RS485, supporting Modbus RTU, CANopen, and PLC/SCADA integration.
- Edge Preprocessing: Built-in RTOS supports 1024-point FFT in under 1 ms; includes 16GB eMMC and 1TB SSD support.
- Robust EMI Design: IP65 metal shielding and power filtering achieve −60 dB@10 MHz signal isolation.
Application Scenarios – Laser Wind Lidar Signal Acquisition: 500 MSPS sampling rate, 14-bit resolution, and anti-interference design to support high-frequency echo acquisition and real-time processing for laser wind lidar. Ideal for applications such as meteorological monitoring and wind profile measurement.
3.Choose Smartgiant for More Efficient and Reliable Data Acquisition and Transmission
In the world of data acquisition, selecting the right interface and DAQ solution is critical—it determines whether your measurements are effectively transformed into actionable digital assets. This article has explored how USB, Ethernet, PCIe, and wireless technologies each serve different needs, and how Smartgiant integrates these advanced interfaces into a diverse product lineup.
From the ultra-fast, low-latency SG1227 PCIe card to the modular and real-time high-speed data acquisition module, and the industrial-grade, edge-processing SG2168 DAQ Box, Smartgiant offers comprehensive solutions tailored for everything from lab research to harsh industrial deployments.
Choose Smartgiant’s DAQ solutions today—
Let every piece of collected data reach your computer efficiently through a high-performance “bridge,” opening a new dimension of precise sensing and intelligent decision-making.
Contact Us
Smartgiant Technology 1800 Wyatt Dr, Unit 3, Santa Clara, CA 95054.
Email: info@smartgiant.com
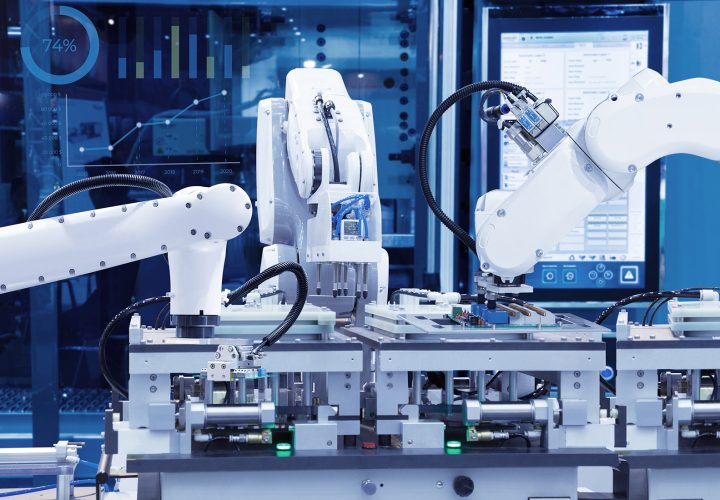
Contact Us
Smartgiant Technology 1800 Wyatt Dr, Unit 3, Santa Clara, CA 95054.
Email: info@smartgiant.com
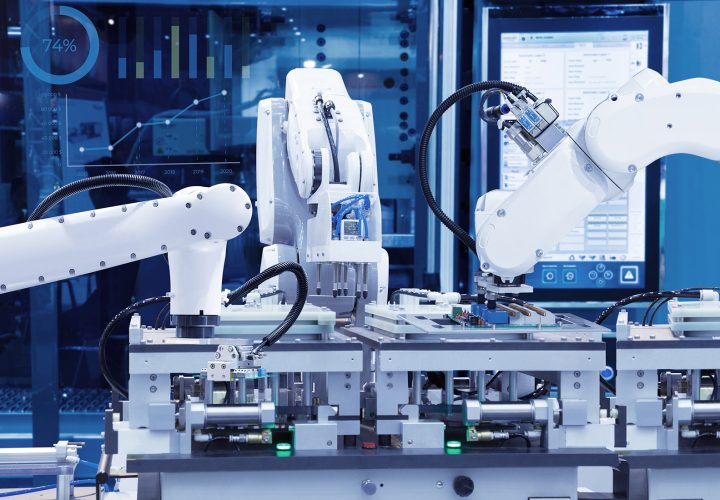